Predictive Maintenance als zentraler Baustein der Industrie 4.0
Am 30. November 2017 fand das FFHS Business Breakfast erstmals in Bern statt. Es war auch das erste Business Breakfast, welches live übers Internet übertragen wurde. Die Teilnehmenden diskutierten darüber, wie Daten beim Unterhalt von Maschinen oder Geräten, Schäden erkennen können, bevor sie zu einem Fehlverhalten führen.
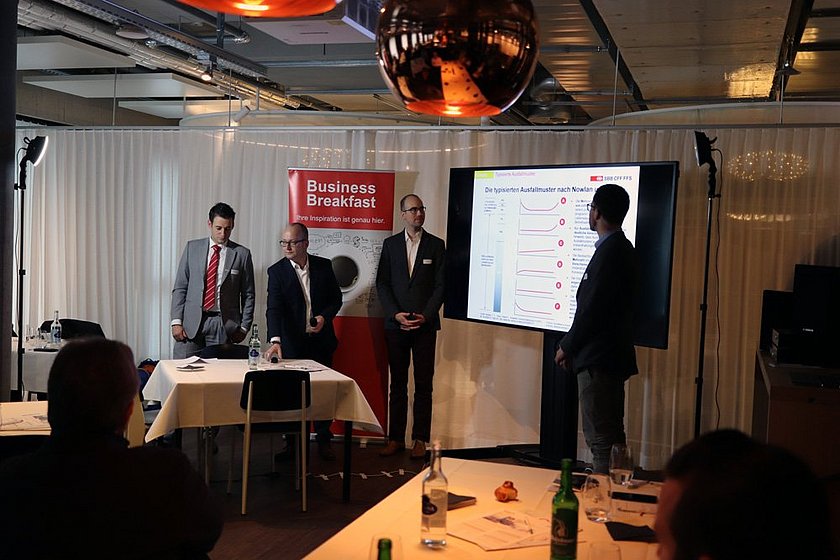
David Gemmet, Urs Gehrig, Philipp Elbel und Sebastian Straus über Predictive Maintenance.
Wie aber funktioniert die vorhersagende Art des Unterhalts – oder im Jargon «Predictive Maintenance» – genau? Grundsätzlich geht es darum, Unterhaltsarbeiten bereits ausführen zu können, bevor etwas kaputtgeht.
Allerdings: Predictive Maintenance ist kein Allheilmittel und auf die ganz grossen Kosteneinsparungen darf man auch nicht hoffen, gab Urs Gehrig zu bedenken. Er leitet bei der SBB das Competence Center Predictive Maintenance und zeigt eindrücklich, dass Predictive Maintenance zwar tatsächlich eine Rolle spielen kann, aber nicht die Hauptrolle beim Unterhaltsmanagement besetzt.
Bouquet der Instandhaltungsmethoden
Damit einig gingen auch Sebastian Straus und Philipp Elbel. Die beiden FFHS-Dozenten unterrichten im MAS Business & IT-Consulting respektive im CAS Digitale Unternehmenskommunikation und zeigten in ihrem Input-Referat, dass man Predictive Maintenance im Kontext betrachten muss. Sie skizzierten vier Stufen von Unterhaltsbestrebungen in einer Firma:
- Reaktive Instandhaltung: Instandhaltung passiert, wenn etwas kaputt gegangen ist (z.B. unerwarteter Motorschaden).
- Zeitabhängige Instandhaltung: Instandhaltungsarbeiten werden in regelmässigen Intervallen vorgenommen. Wie gross das Intervall sein muss, basiert auf Erfahrungswerten (z.B. jährlicher Service).
- Zustandsabhängige Wartung: Sensoren liefern Messdaten zum Zustand einer Maschine. Basierend auf diesen Messwerten wird eine Wartungsaktion durchgeführt (z.B. leere Tankanzeige).
- Vorausschauende Wartung (Predictive Maintenance): Wie bei zustandsabhängiger Wartung werden an der Maschine Daten erhoben. Allerdings wird nicht direkt abgelesen, wann eine Wartungsaktion fällig wird, sondern Algorithmen errechnen – meist basierend auf einer Vielzahl von Datenquellen – die Wahrscheinlichkeit, wann mit einem Schaden zu rechnen bzw. wann eine Wartung vorzunehmen ökonomisch Sinn machen könnte.
Straus und Elbel betonen, dass beim Einrichten eines vorausschauenden Wartungssystem auf Vieles Rücksicht genommen werden muss: Wo lassen sich Daten erfassen? Wie funktioniert die Datenerfassung? Wo werden Daten abgelegt? Und: Wie wird aus Datenbergen nutzbare Information? Alle diese Fragen müssen geklärt werden. Was wiederum bedeutet: «Predictive Maintenance kostet initial Geld.»
Noch riskant, langfristig lohnenswert
Gerade Early-Adopters, also Firmen, die früh auf die Automatisierung des Unterhalts setzen, riskieren viel. Denn noch fehlen Standards bei den Sensoren, bei der Kommunikation zwischen den Datenquellen und bei den Plattformen, auf denen Daten abgelegt werden. Frühumsteiger müssen also vieles selber aufbauen, was später standardisiert werden könnte. Noch ist alles im Fluss.
Langfristig aber, sind die beiden Dozierenden überzeugt, lohnt sich der Ansatz. Wenn eine Bahn keine starren Wartungsintervalle und weniger unvorhergesehene Schäden berücksichtigen muss, kann sie abgestellte Reserve-Loks im Betrieb einsetzen. Oder sie kann sie verkaufen. So oder so ist ein Produktivitätszuwachs die Folge von – zuverlässig funktionierender – Predictive Maintenance.
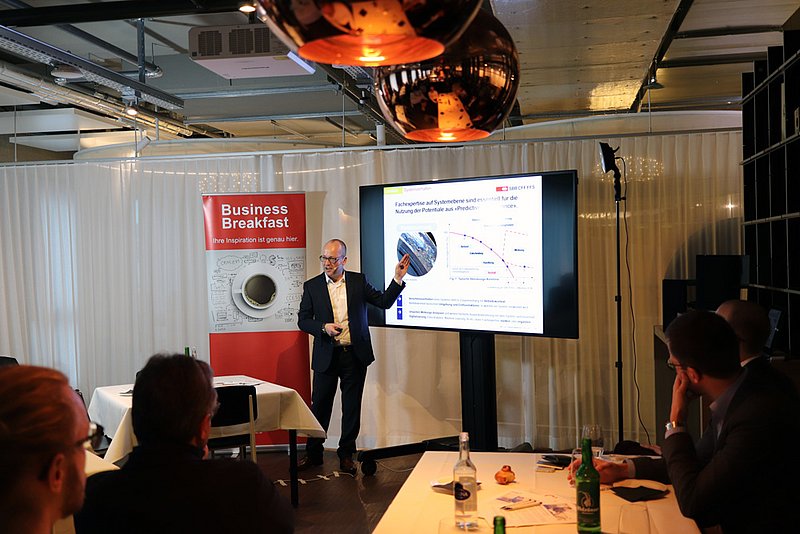
Urs Gehrig sieht Predictive Maintenance bei der SBB als eine Stimme im Chor der Maintenance-Mittel.
Mehr Effizienz ist Pflicht
Effizienzgewinne sind – gerade im Eisenbahnbereich – aber längst Pflicht geworden. «Wir erwarten in den nächsten Jahren weiterhin starkes Wachstum bei der Bahn. Und das trotz des schon stark belasteten Eisenbahnnetzes», erklärt Urs Gehrig. Das Wachstum bei den Passagierzahlen wirke sich auf den Instandhaltungsaufwand Wachstum bei der Instandhaltung und dieser auf die Kosten aus. Man sei deswegen bestrebt, Instandhaltungsarbeiten an allen Fronten zu optimieren. «Predictive Maintenance ist ein Teil unserer präventiven Instandhaltungsmassnahmen».
Manche Schäden können durch traditionelle Maintenance-Verfahren vorweggenommen oder bei nicht-sicherheitsrelevanten Dingen sogar reaktiv behoben werden. Bei Defekten, aber, die sich nur schwer vorhersagen lassen, können Daten, kombiniert mit einem cleveren Algorithmus, Abhilfe schaffen.
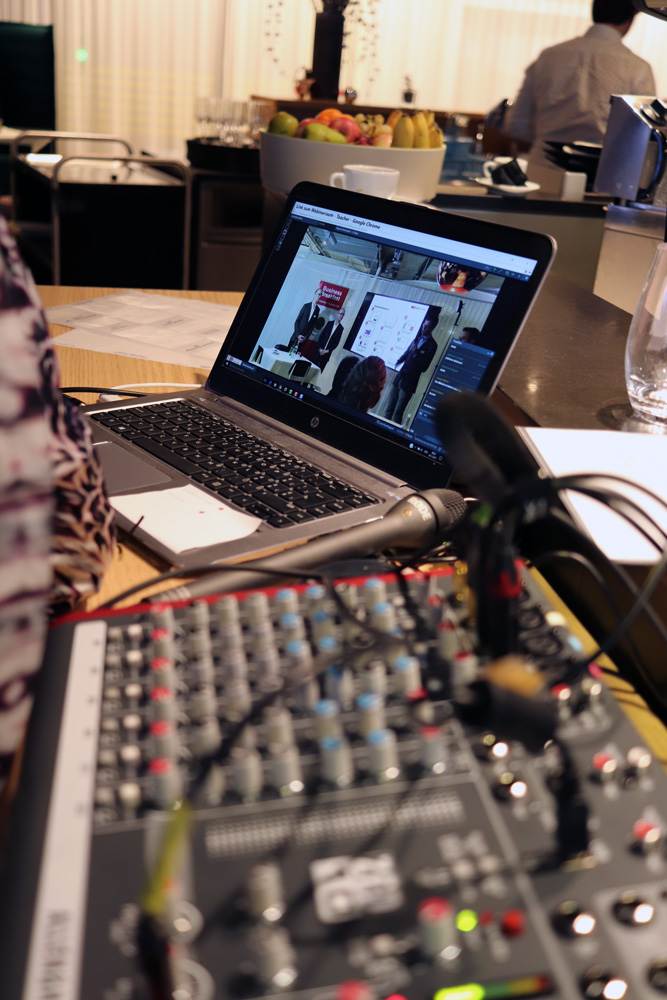
rstmals fand das 13. Business Breakfast auch online als Remote-Veranstaltung statt.
Voraussetzung Lernwille
Wer sich vornimmt, Big Data im Unterhalt seiner Maschinen einzusetzen, muss lernwillig sein, so Urs Gehrig. «Bei der SBB haben wir ein Team gebildet, welches im Bereich Predictive Maintenance Proofs of Concept erarbeitet, also testet, ob sich eine Idee umsetzen lässt.» Aber auch auf der Stufe des Service-Mitarbeitenden muss sich Einiges tun, so Gehrig. «Es ist wichtig, dass Mitarbeitende offen bleiben. Eine gewisses Interesse an neuen Technologien schadet sicher auch nicht». In Gesprächen mit Teilnehmenden stellte sich heraus, dass genau dieser Wandel in den Berufsbildern, Verantwortungen und Aufgaben sowie das damit verbundene Change Management eine der grossen Herausforderungen ist.
Predictive Maintenance sei eine Chance, war der Grundtenor. Zwar sei der Einstieg noch relativ schwierig und Unternehmen müssten viel Vor- und Aufbauarbeit leisten. Wenn sie dies aber täten, seien die Benefits durchaus vorhanden. Arbeit gebe es, bestätigte Urs Gehrig zum Schluss, auch im Zeitalter von Predictive Maintenance ausreichend.
Präsentationen
Präsentation David Gemmet, Studiengangsleiter 4.0
Präsentation Sebastian Straus und Philipp Elbel, Dozenten FFHS
Präsentation Ulrich Gehrig, SBB