Wenn Künstliche Intelligenz die industrielle Metallverarbeitung optimiert
Die FFHS-Forscherinnen Prof. Dr. Martina Perani und Prof. Dr. Beatrice Paoli zeigen in einer Studie, wie Künstliche Intelligenz (KI) in der Lasermetallbeschichtung eingesetzt werden könnte, um den industriellen Fertigungsprozess effizienter zu machen.
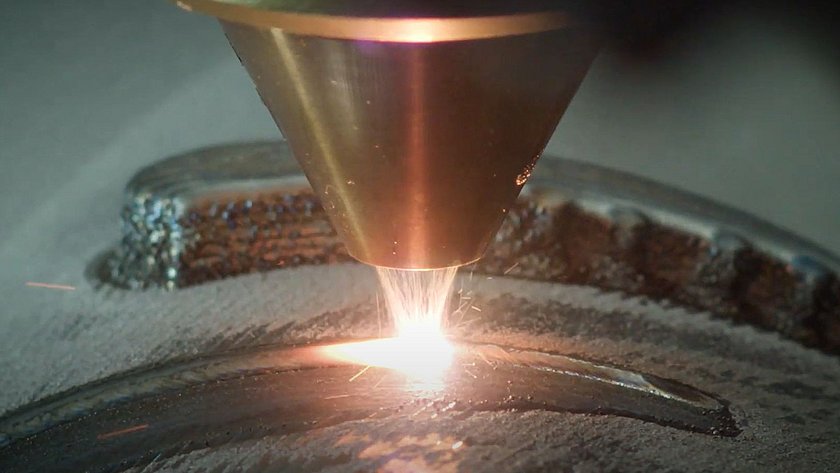
Die Technologie der additiven Fertigung von Metallen entwickelt sich ständig weiter und wird dank dem Einsatz von künstlicher Intelligenz noch viel präziser und effizienter werden. (Bild: F.W. Gartner)
Das Lasermetallbeschichten (Laser Metal Deposition LMD) ist eine Technologie, die wegen ihres immensen Potenzials auf grosses Interesse in der Industrie stösst. Die Einbindung von KI wäre für den 3D-Druck in der Industrie eine höchst effiziente Weiterentwicklung. In der Luftfahrtbranche werden beispielsweise bei Motoren, die bei der Boeing 777X verwendet werden, über 300 Einzelteile mittels 3D-Druck-Verfahren angefertigt. Durch den additiven Fertigungsprozess unter Einsatz von KI würde noch mehr Zeit eingespart als bisher. Aber auch beim Material könnte mit bis zu zehnmal weniger Verlust gerechnet werden.
Bei LMD wird ein Hochleistungslaser als Wärmequelle eingesetzt. Während diesem Verfahren wird durch Aufschmelzen und gleichzeitiges Auftragen von nahezu beliebigen Materialien eine Oberflächenschicht erzeugt. Der Zusatzwerkstoff kann entweder in Pulverform (Metallpulver) oder mit einem Schweissdraht zugeführt werden. Beim Lasermetallbeschichten mit Pulver erwärmt der Laser das Werkstück mit einem Laserstrahl und schmilzt es lokal auf. Gleichzeitig wird ein mit feinem Metallpulver vermischtes Inertgas eingeleitet. Das Metallpulver schmilzt an der erhitzten Stelle und wird mit der Oberfläche des Werkstücks verbunden.
Forschung führt zu effizienteren Fertigungsprozessen
Die Forschenden haben nun KI eingesetzt, um die Grösse von Teilen zu steuern, die durch das 3D-Drucken (additive Fertigung) mit Pulvern aus einer Nickel-Chrom-Legierung (Inconel 718) beschichtet werden. Dank des elaborierten KI-Modells kann die gewünschte Grösse der hergestellten Teile schon während des Beschichtungsprozesses besser kontrolliert sowie gegebenenfalls korrigiert und ein zusätzlicher Arbeitsschritt vermieden werden. Dadurch soll künftig in der industriellen Produktion effizienter gearbeitet werden können. «Wir konnten mit unserer Studie beweisen, dass künstliche Intelligenz für die Modellierung des LMD-Verfahrens grundsätzlich geeignet ist. Jetzt können wir unseren Fokus auf komplexere Objektstrukturen legen», sagt Prof. Dr. Martina Perani, Forschungsfeldleiterin «Data Science für Energie, Umwelt und Materialien» im Laboratory for Web Science der FFHS.
Das grosse Potenzial
Wenn man während dem Beschichtungsprozess bereits Änderungen vornehmen könnte, wären in der Folge weniger Schritte nötig, um die Grösse der Einzelteile zu korrigieren. Die Forschung ist aber heute noch nicht so weit, dass man diese in Echtzeitsteuerung durchführen kann, da bis jetzt nur sehr einfache Teilchen, sogenannte Spuren, analysiert werden konnten. Dennoch beweist die Forschung, dass sich diese Methode für den beabsichtigten grösseren Zweck eignet. Zudem werden die einzelnen Teile künftig leichter sein, was etwa zu Kosteneinsparungen beim Treibstoff führt. Komplexere Objekte können direkt und mit weniger Zwischenschritten hergestellt und repariert werden – und behalten zugleich ideale mechanische Eigenschaften bei. Die Forschenden sind nun daran, dass künftig auch «echte Stücke» optimiert werden können. Ihre Forschungsarbeit wurde in der Fachpublikation «Robotics and Computer-Integrated Manufacturing» veröffentlicht.